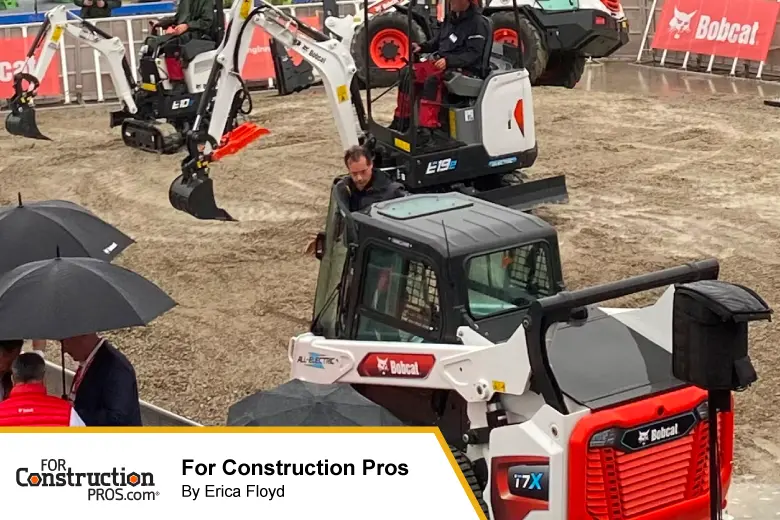
It’s Electric: How Diversifying Fleets Can Help Contractors Win Bids
Indoor work, such as demolition, requires cleaner air and quieter machines to do the job effectively, quickly and cleanly. There seems to be no better match for demolition in close quarters, with walls as space constraints, than compact electric equipment. Equipment Today recently sat down with Joseph D’Amato of D’Amato Construction Company, Inc., based in Connecticut, to discuss the contractor’s use of the Volvo ECR25 fully electric mini excavator, which has all auxiliary hydraulics, for interior demolition and construction.
“I believe it’s a 6500-pound machine and we’re using it for primarily interior wall and interior dismantling, interior excavation for new sewer trenches and demolition in buildings, and renovating,” D’Amato said. “It’s worked it’s working very well…for its application, it’s second to none. It’s perfect for the position that you need to run half a day inside, say, a high-end facility where you can’t have any fumes or anything of that nature.”
“It’s perfect for that situation because a lot of times when we’re in some of our dismantling renovation jobs, we’re in a building that we have to work off hours because we need to put extensive equipment inside, and unfortunately there is not the capacity of electric machines yet, in that those applications cannot yet handle our bigger specialty attachments,” D’Amato explained. “So, we can plan accordingly to do that stuff off hours,” and use the ECR25 during on hours, according to facility requirements.
For time efficiency, the D’Amato crew created a cart with a transformer on it that follows the machine so that they can put a higher rate of charge on the electric excavator wherever it is on the worksite.
“We’ve also used the 110-volt charging—we’ve used all the forms of charging—and the 110-volt charging when we’re working, you know, intermittently throughout the day, doing sewer trenches, stuff like that, the one 110-volt charger is plenty, because we’re able to let it charge overnight and arrive in the morning to it fully charged,” D’Amato said. “So, for on-and-off use during the day, 110-volt charging is more than sufficient for our uses of the machine. We’re not having any issues with not having enough battery life in that application or anything along those lines.”
Battery charging of electric equipment in general has been a large question mark for many contractors hesitant to adopt the new technology. However, as Equipment Today reported last March 2022, charging solutions will be largely influenced by power sources available on the jobsites.
“Many battery-electric vehicles (BEVs) offer a choice of single- or three-phase charging,” former Equipment Today writer and trucks editor Curt Bennink wrote. “There are key differences. With single phase, power flows through a single conductor, while three phase flows through three conductors. This means three-phase charging allows a higher charging capacity than the single-phase — almost three times. Most U.S. households are powered by single-phase electricity, with two hot wires each carrying 120 volts and a ground wire. The two hot wires produce a total of 240 volts for heavy appliances.”
Available charging options can currently be divided into three different levels:
-
- Level 1 uses the standard grounded 120-volt AC outlet, which can be found anywhere in the United States. This also provides the slowest rate of charge.
-
- The Level 2 charger uses a 240-volt AC outlet. It offers twice the charge rate of a Level 1 charger.
-
- A Level 3 fast charger uses DC current rather than alternating household current. It charges through a high-power 480-volt plug often hooked up directly to the electrical grid.
The method of charging will affect battery life. According to Volvo Construction Equipment, the best for maximizing battery life is AC Level 2 charging, which is slow charging compared to DC rapid charging. But the best choice will depend on customer needs.
Like D’Amato Construction, KATO Compact Excavator Sales also uses the 110-volt charging option on their fully electric units, Bart Dehaven, KATO-CES national sales representative, told Equipment Today last year.
KATO-CES supplies a specialty charger for each model, which is specific to that machine.
“The only thing that we have run into is, it is a 110-volt outlet, but it requires 20 amps,” DeHaven said. “That’s been a little bit of a learning curve. It does require that heavier amperage to charge it.”
D’Amato Construction focuses mostly on commercial construction, including private sector, Department of Defense healthcare facilities, water treatment plants and other specialty, unique job applications that require intricate planning. While they do not have many government contracts, D’Amato said he foresees more business coming in due to the electric excavator’s abilities to operate cleanly and quietly. D’Amato also expressed interest in purchasing a larger electric excavator with compatible attachments from Volvo, if available. Other interested contractors should keep an eye out for any new product releases at the upcoming 2023 CONEXPO-CON/AGG trade show.
D’Amato pointed out that electric machines have a cost advantage for the customer, as well, particularly for the type of work D’Amato Construction engages in, in specialty commercial projects that often have noise and emissions restrictions.
“Off hours work…always costs the end user more – the customer – because you’re putting crews on shift at night as opposed to day. The overhead is very different and downtime is more likely overnight because you don’t have the availability of parts, service, other trade suppliers at night,” D’Amato explained. “When you’re able to do the work during the day because you have an electric machine as opposed to carbon emissions machine you can do the work inherently cheaper.”
“The bidding process makes us be able to come in with a lot more competitive price knowing we have the resources and the ability to do it in that manner,” he said.
As of right now, in the state of Connecticut, D’Amato Construction is not facing stringent environmental emissions requirements yet, in comparison to California. Connecticut recently passed legislation on emissions compliance leading to Tier 4 compliance, like California has. Fully electric equipment may be the future of indoor construction and demolition, D’Amato hinted, whether states are saying it aloud or not. Small electric engines will eventually give way to the design and manufacturing of mid-size electric engines and beyond, D’Amato predicts.
D’Amato said he typically prefers simple machines that are easy to fix, but “when it comes to the certain applications and stuff like that, if it’s the better thing, it’s the better thing.”
Bobcat Company also unveiled its all-electric Bobcat T7X compact track loader (CTL) at the Consumer Electronics Show 2022 in Las Vegas on January 4, 2022, Equipment Today reported last year. This CTL is the first machine of its kind to fully eliminate all hydraulics and components, resulting in a machine that is 10 times quieter than its diesel-hydraulic equivalent
The unique design of the T7X has nearly 50% fewer parts than the diesel-hydraulic version. The traditional hydraulic work group has been completely replaced with an electrical drive system consisting of electric cylinders and electric drive motors, which means virtually no fluids. Only one quart of eco-friendly coolant is required compared to 57 gal. of fluid in the equivalent diesel-hydraulic model. The machine promises to lower daily operating costs when considering the reduction in annual maintenance costs and elimination of diesel, engine oil, diesel exhaust fluid and hydraulic parts.
“The machine is fully battery powered and is designed to outperform its diesel counterparts,” says Joel Honeyman, vice president of global innovation, Bobcat Company. “The machine is more intelligent and productive with electric propulsion. It’s quiet with high-performance torque, and it’s more powerful than anything that has come before — all while eliminating carbon emissions.”
While the exact run time will vary by application, the use of intelligent work modes can allow up to four hours of continuous operation time and a full day of operation during intermittent use.
Two-way telematics communication provides integral data about the performance of the machine, along with operator-focused data to change machine preferences, tune the performance to certain job situations and upgrade product features. This includes variable drive speed at full torque and other features not possible with a diesel-hydraulic machine.
“We employ different work modes that we’ve developed through software, depending upon the task, to help conserve battery power,” says Honeyman. “We have an Eco mode, an Advanced mode and even a Beast mode, which provides short bursts of full instantaneous torque to the drive system when needed.”
Bobcat collaborated with Moog Inc., a worldwide developer of motion control components and systems, to speed up the pace of research and development of the electronic control capabilities of the T7X. The removal of the hydraulic system requires a different approach from the attachment side, and Bobcat is currently working on launching a line of fully electric attachments.
The T7X has enthusiastic support Sunbelt Rentals, which has more than 1,025 locations in North America. Sunbelt recently entered into a strategic partnership to make a significant investment in a large fleet of Bobcat T7X CTLs and electric compact excavators, which were co-branded and made available in 2022.
Similarly, “Volvo CE holds a national cooperative purchasing contract allowing state and local governments to purchase our full product offering, including our electric equipment lineup, direct off contract,” said Kathy Tedone, Volvo State & National Buying Contract Manager. “Volvo CE also has a program in place extending government pricing to private contractors who hold a firm-fixed Pricing contract for federal and state-funded projects, which includes access to our electric equipment offering. As other alternatively powered equipment becomes available, it will be added to the program.”
According to D’Amato, the availability of size applications will be an ongoing endeavor to continue to build fully electric fleets. There currently are not 15 different weight class machines available to suit every contractor’s needs, but perhaps there will be soon, he said.
While Connecticut does not have state government tax or credit incentives for contractors like the size of D’Amato construction to build all-electric fleets, buying other electric vehicles for construction jobsites certainly has its advantages, D’Amato said.
“When we were ordering some new trucks, we purchased an electric vehicle and that moved us ahead over a year on our build dates,” D’Amato said. “In general, in the electric world, we gain the ability to take advantage of—purchase an electric vehicle—to get our get our build dates for some [bids and projects] we’re looking at a lot sooner than everybody else around us.”
“So,” D’Amato finished, “that right there is an incentive.”