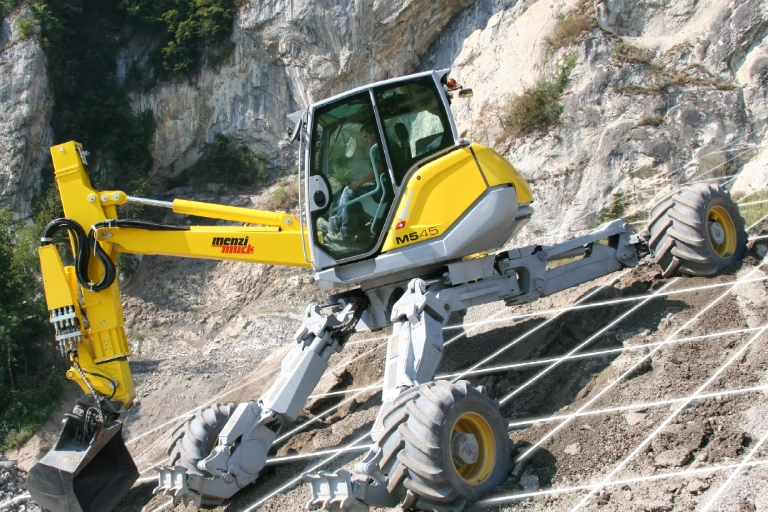
Automating a Spider Excavator to Increase Productivity
Spider excavators, sometimes called walking excavators are a special breed of machine designed to work in difficult terrain such as mountainous areas, wild riverbeds, and mountain roads. The cutting-edge machine has been around for fifty years and is used for challenging work such as mulching steep slopes, driving in riverbeds, removing mudslides and felling/processing trees. In emergency situations, this machine can be the first line of defense to protect humans and infrastructure from rockfalls, avalanches, and erosion.
Challenges
Because there is no transmission on this machine, the steering system manages drive as well through an electric actuator and an electric traction motor and includes various software-generated gear ratios to approximate the drive feel operators are used to while making the steering on the machine much more responsive and less tiring. At least for these first electric loaders, Komatsu says they are fine tuning the steering system to have a very similar feel to a hydraulically driven machine. The difference is that through software, Komatsu can offer finer control of the machine with increased speed.
The electric traction motor is a particularly interesting aspect of this system as it allows Komatsu to integrate elements of automation more seamlessly into operation of the machine. For instance, if the machine senses an operator pushing into a pile, the loader would initiate a friction control or an anti-tire-slip function that would allow you to more smoothly dig into the pile and efficiently fill a bucket.
The system also would allow Komatsu to easily implement joystick control on the machine, though joysticks are not as popular on compact loaders as they are on the larger size loaders, redesigning the electrical architecture of the machine does open up that move from pilot controls to E/H controls. The system also includes power electronics, a system control computer, and, of course, a battery and battery management system.
Solutions
Moog engineers designed a highly dynamic hydraulic system, enabling the operator to automatically balance the machine, while driving through difficult terrains.
The success of the Automated Chassis Control solution was a direct result of using a dynamic simulation of machine applications that started with a layout of the control structure of the hardware and software. The simulation generates repeatable stress tests to investigate the system behavior in critical situations. Long before the actual physical system exists, we can specify the system, subsystem, and component level requirements. Advanced modeling also reduces any big surprises with the first prototype. We can help customers understand and clarify suspicious behavior of the actual system. Repeatable reproduction of specific scenarios allows analysis and quick understanding of physical effects to quickly and effectively solve the problem.
Moog’s innovation and state-of-the-art technology involved embedded real-time controller structures and blocks directly in Matlab/Simulink without direct coding. The controllers can be tested, qualified, and validated in a comfortable offline simulation environment without the typical limitations of real-time embedded systems.
Fives Step to Advanced Control for Next-Generation Machines
- Our experienced engineers completed a technology assessment and determined that current mobile hydraulic equipment and controller solutions would not meet the requirements of the project.
- Engineers identified a state-of-the-art controller structure that could be used with robust industrial hydraulic equipment and fulfill the dynamic requirements.
- To prove the vehicle stability, Moog engineers built a simulation model for quick design iterations to simulate the actuation system’s characteristics and investigate complete vehicle dynamics. The specifications required for the components were easily defined by the simulation model, saving time and money.
- Moog built and installed prototypes of the Automated Chassis Stabilization Control System including Integrated Smart Actuators that included Safety and Control Functions based on Industrial Servo Valves.
- Final tests confirmed our state-of-the-art smart control structures provide a highly dynamic active suspension system for mobile machines using rugged industrial components.
Results: Enabling New Business Models
While the original goal was to benefit the operator, the OEM found the ultimate solution had many unforeseen benefits for productivity, safety, and the environment. Making the job easier and safer for operators has implications for reduced costs for training, hiring and upskilling employees. Here are some examples of new use cases that the OEM found because of the many advantages this machine has to transform the work of operators and job sites.
New Business Model: Teleoperation in Dangerous Environments
Machines are now teleoperated in rockfall areas and abandoned ammunition depots to keep drivers outside the danger zone. Before installing the Moog Automated Chassis Stabilization manual remote operation was simply not possible due to the complexity of operating the twelve axes. Today with the Automated Chassis Control maintaining the machine’s stability, many new business models are possible, opening the door to a range of applications where protecting operators and the environment are essential.
Greater Productivity & Reduced Environmental Impact: Excavating and Landscaping in Extreme Terrains
The Automated Chassis Control maintains the contact force of all wheels providing stability for the machine and enabling a quicker transfer between job sites. The automated control reduces the impact force of each individual wheel by distributing the force to all wheels resulting in minimizing the impact to the soil and the ground vegetation.
Greater Operator Productivity & Safety: Municipal Maintenance Service of Riverbanks
Many drivers were reluctant to drive in riverbeds because they lacked visibility of the ground and could not adapt to conditions quickly. The Automated Chassis Control maintains the vehicles balance so the operator focuses full attention on the tool and the job. The result is higher productivity, with work performed faster and better than previously possible.
Greater Operator Productivity and Safety: Forestry in Uneven and Dangerous Terrain
Tree harvesting is hard work for operators and demands absolute attention of your most skilled driver. The Automatic Chassis Control stabilizes the machine allowing the machine operator to focus on the processor’s head, so the job is executed faster and is less tiring for the operator. Additionally, distributing the force to all wheels minimizes the impact on the soil and the surrounding trees.
Greater Operator Productivity and Safety: Civil Engineering in Mountainous Areas
Drilling anchor holes for securing roads and railroad tracks is challenging and dangerous work for operators in mountainous areas. Machines equipped with the Automated Chassis Control maintaining the stability of the machine, allowed the driver to stay focused on taking a safe route to the work sites.
The new hydraulic system resulted in so many advantages over the traditional solution that it transformed work for operators and even the most challenging job sites. What can this kind of advanced system do for your machine?